দৃঢ়ীকরণের সময় গ্যাসের ফাঁদে ফেলার ফলে সচ্ছলতা, গহ্বরের ধরণের বিচ্ছিন্নতা, এমআইজি ওয়েল্ডিং-এর একটি সাধারণ কিন্তু কষ্টকর ত্রুটি এবং বিভিন্ন কারণ সহ একটি। এটি আধা-স্বয়ংক্রিয় বা রোবোটিক অ্যাপ্লিকেশনগুলিতে উপস্থিত হতে পারে এবং উভয় ক্ষেত্রেই অপসারণ এবং পুনরায় কাজ করার প্রয়োজন - যা ডাউনটাইম এবং বর্ধিত খরচের দিকে পরিচালিত করে।
ইস্পাত ঢালাইয়ে পোরোসিটির প্রধান কারণ হল নাইট্রোজেন (N2), যা ওয়েল্ডিং পুলে জড়িত। যখন তরল পুল ঠান্ডা হয়, N2 এর দ্রবণীয়তা উল্লেখযোগ্যভাবে হ্রাস পায় এবং N2 গলিত ইস্পাত থেকে বেরিয়ে আসে, বুদবুদ (ছিদ্র) গঠন করে। গ্যালভানাইজড/গ্যালভানিয়াল ওয়েল্ডিং-এ, বাষ্পীভূত জিঙ্ককে ওয়েল্ডিং পুলে আলোড়িত করা যেতে পারে, এবং পুল শক্ত হওয়ার আগে পালানোর পর্যাপ্ত সময় না থাকলে, এটি ছিদ্র তৈরি করে। অ্যালুমিনিয়াম ঢালাইয়ের জন্য, সমস্ত পোরোসিটি হাইড্রোজেন (H2) দ্বারা সৃষ্ট হয়, যেভাবে N2 ইস্পাতে কাজ করে।
ঢালাই ছিদ্র বাহ্যিকভাবে বা অভ্যন্তরীণভাবে প্রদর্শিত হতে পারে (প্রায়ই সাব-সারফেস পোরোসিটি বলা হয়)। এটি জোড়ের একক বিন্দুতে বা পুরো দৈর্ঘ্য বরাবর বিকাশ করতে পারে, যার ফলে দুর্বল ঝালাই হয়।
ছিদ্রের কিছু মূল কারণ কীভাবে শনাক্ত করা যায় এবং কীভাবে সেগুলো দ্রুত সমাধান করা যায় তা জেনে গুণমান, উৎপাদনশীলতা এবং নীচের লাইন উন্নত করতে সাহায্য করতে পারে।
দরিদ্র শিল্ডিং গ্যাস কভারেজ
দুর্বল শিল্ডিং গ্যাস কভারেজ হল ঢালাইয়ের ছিদ্রের সবচেয়ে সাধারণ কারণ, কারণ এটি বায়ুমণ্ডলীয় গ্যাস (N2 এবং H2) ওয়েল্ড পুলকে দূষিত করতে দেয়। সঠিক কভারেজের অভাব বিভিন্ন কারণে ঘটতে পারে, যার মধ্যে কিন্তু সীমাবদ্ধ নয় দুর্বল শিল্ডিং গ্যাস প্রবাহের হার, গ্যাস চ্যানেলে লিক হওয়া, বা ওয়েল্ড সেলে অত্যধিক বায়ু প্রবাহ। খুব দ্রুত ভ্রমণের গতিও অপরাধী হতে পারে।
যদি কোনো অপারেটর সন্দেহ করে যে দুর্বল প্রবাহ সমস্যা সৃষ্টি করছে, তাহলে রেট পর্যাপ্ত তা নিশ্চিত করতে গ্যাস ফ্লো মিটার সামঞ্জস্য করার চেষ্টা করুন। স্প্রে ট্রান্সফার মোড ব্যবহার করার সময়, উদাহরণস্বরূপ, প্রতি ঘন্টায় 35 থেকে 50 ঘনফুট (cfh) প্রবাহ যথেষ্ট। উচ্চ অ্যাম্পেরেজগুলিতে ঢালাইয়ের জন্য প্রবাহের হার বৃদ্ধির প্রয়োজন, তবে হারটি খুব বেশি সেট না করা গুরুত্বপূর্ণ। এর ফলে কিছু বন্দুকের নকশায় অশান্তি দেখা দিতে পারে যা গ্যাস কভারেজকে রক্ষা করে।
এটি লক্ষ করা গুরুত্বপূর্ণ যে ভিন্নভাবে ডিজাইন করা বন্দুকগুলির বিভিন্ন গ্যাস প্রবাহের বৈশিষ্ট্য রয়েছে (নীচের দুটি উদাহরণ দেখুন)। উপরের ডিজাইনের জন্য গ্যাস প্রবাহের হারের "মিষ্টি স্পট" নীচের ডিজাইনের তুলনায় অনেক বড়। ওয়েল্ড সেল সেট আপ করার সময় এটি এমন কিছু যা একজন ওয়েল্ডিং ইঞ্জিনিয়ারকে বিবেচনা করতে হবে।
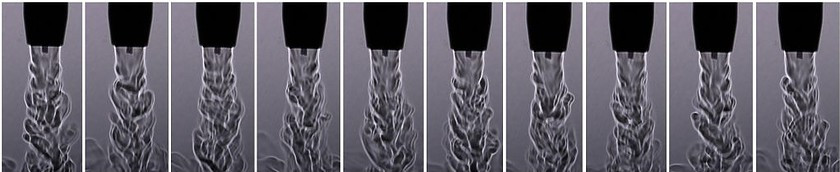
নকশা 1 অগ্রভাগের আউটলেটে মসৃণ গ্যাস প্রবাহ দেখায়
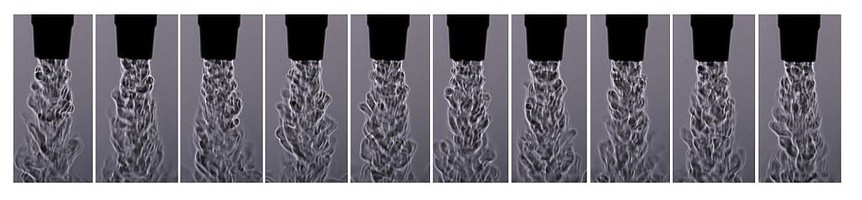
নকশা 2 অগ্রভাগের আউটলেটে অশান্ত গ্যাস প্রবাহ দেখায়।
এছাড়াও গ্যাসের পায়ের পাতার মোজাবিশেষ, জিনিসপত্র এবং সংযোগকারীর ক্ষতির জন্য পরীক্ষা করুন, সেইসাথে MIG ওয়েল্ডিং বন্দুকের পাওয়ার পিনের ও-রিংগুলি। প্রয়োজনে প্রতিস্থাপন করুন।
ওয়েল্ড সেলের অপারেটর বা যন্ত্রাংশগুলিকে ঠান্ডা করার জন্য ফ্যান ব্যবহার করার সময়, খেয়াল রাখবেন যে সেগুলি সরাসরি ঢালাইয়ের জায়গায় নির্দেশিত না হয় যেখানে তারা গ্যাস কভারেজ ব্যাহত করতে পারে। বাহ্যিক বায়ু প্রবাহ থেকে রক্ষা করতে ওয়েল্ড কক্ষে একটি পর্দা রাখুন।
একটি সঠিক টিপ-টু-কাজ দূরত্ব রয়েছে তা নিশ্চিত করতে রোবোটিক অ্যাপ্লিকেশনগুলিতে প্রোগ্রামটিকে পুনরায় স্পর্শ করুন, যা সাধারণত ½ থেকে 3/4 ইঞ্চি হয়, আর্কের পছন্দসই দৈর্ঘ্যের উপর নির্ভর করে।
সবশেষে, ধীর ভ্রমণের গতি যদি ছিদ্র বজায় থাকে বা আরও ভাল গ্যাস কভারেজ সহ বিভিন্ন ফ্রন্ট-এন্ড উপাদানগুলির জন্য একটি এমআইজি বন্দুক সরবরাহকারীর সাথে পরামর্শ করুন
বেস মেটাল দূষণ
বেস ধাতু দূষণ হল ছিদ্র হওয়ার আরেকটি কারণ - তেল এবং গ্রীস থেকে মিল স্কেল এবং মরিচা পর্যন্ত। আর্দ্রতা এই বিচ্ছিন্নতাকে উত্সাহিত করতে পারে, বিশেষ করে অ্যালুমিনিয়াম ঢালাইয়ে। এই ধরনের দূষকগুলি সাধারণত বাহ্যিক ছিদ্রের দিকে পরিচালিত করে যা অপারেটরের কাছে দৃশ্যমান। গ্যালভানাইজড ইস্পাত সাবসারফেস পোরোসিটির জন্য বেশি প্রবণ।
বাহ্যিক পোরোসিটি মোকাবেলা করার জন্য, ঢালাই করার আগে বেস উপাদানটি পুঙ্খানুপুঙ্খভাবে পরিষ্কার করতে ভুলবেন না এবং একটি ধাতব-কোরড ওয়েল্ডিং তার ব্যবহার করার কথা বিবেচনা করুন। এই ধরনের তারে কঠিন তারের তুলনায় ডিঅক্সিডাইজারের মাত্রা বেশি থাকে, তাই এটি বেস উপাদানের অবশিষ্ট দূষকগুলির থেকে বেশি সহনশীল। এইগুলি এবং অন্য কোনও তারগুলিকে সবসময় গাছের তুলনায় অনুরূপ বা সামান্য বেশি তাপমাত্রার শুষ্ক, পরিষ্কার জায়গায় সংরক্ষণ করুন। এটি করা ঘনীভবন কমাতে সাহায্য করবে যা ওয়েল্ড পুলে আর্দ্রতা প্রবর্তন করতে পারে এবং ছিদ্রতা সৃষ্টি করতে পারে। ঠান্ডা গুদামে বা বাইরে তারগুলি সংরক্ষণ করবেন না।
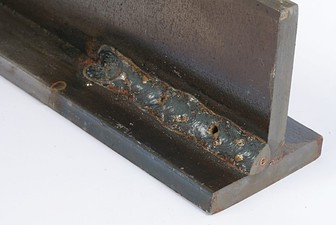
দৃঢ়ীকরণের সময় গ্যাসের ফাঁদে ফেলার ফলে সচ্ছলতা, গহ্বরের ধরণের বিচ্ছিন্নতা, এমআইজি ওয়েল্ডিং-এর একটি সাধারণ কিন্তু কষ্টকর ত্রুটি এবং বিভিন্ন কারণ সহ একটি।
গ্যালভানাইজড ইস্পাত ঢালাই করার সময়, দস্তা ইস্পাত গলে যাওয়ার চেয়ে কম তাপমাত্রায় বাষ্প হয়ে যায় এবং দ্রুত ভ্রমণের গতি ওয়েল্ড পুলকে দ্রুত বরফে পরিণত করে। এটি ইস্পাতে দস্তার বাষ্প আটকাতে পারে, যার ফলে ছিদ্র হয়। ভ্রমণের গতি পর্যবেক্ষণ করে এই পরিস্থিতির মোকাবিলা করুন। আবার, বিশেষভাবে ডিজাইন করা (ফ্লাক্স ফর্মুলা) ধাতব-কোরড তারের কথা বিবেচনা করুন যা ওয়েল্ডিং পুল থেকে দস্তা বাষ্পের পালাতে সাহায্য করে।
আটকানো এবং/অথবা কম আকারের অগ্রভাগ
আটকানো এবং/অথবা ছোট অগ্রভাগও ছিদ্র সৃষ্টি করতে পারে। ওয়েল্ডিং স্প্যাটার অগ্রভাগে এবং যোগাযোগের ডগা এবং ডিফিউজারের পৃষ্ঠে তৈরি হতে পারে যা সীমিত সুরক্ষা গ্যাস প্রবাহের দিকে পরিচালিত করে বা এটি অশান্ত হয়ে উঠতে পারে। উভয় পরিস্থিতিতে অপর্যাপ্ত সুরক্ষা সঙ্গে জোড় পুল ছেড়ে.
এই পরিস্থিতির সংমিশ্রণ হল একটি অগ্রভাগ যা প্রয়োগের জন্য খুব ছোট এবং বৃহত্তর এবং দ্রুত স্প্যাটার তৈরির প্রবণতা। ছোট অগ্রভাগগুলি আরও ভাল যৌথ অ্যাক্সেস সরবরাহ করতে পারে, তবে গ্যাস প্রবাহের জন্য অনুমোদিত ছোট ক্রস-বিভাগীয় অঞ্চলের কারণে গ্যাস প্রবাহকে বাধা দেয়। সর্বদা অগ্রভাগের স্টিকআউটে যোগাযোগের টিপ (বা অবকাশ) এর পরিবর্তনশীলটি মনে রাখবেন, কারণ এটি আরেকটি কারণ হতে পারে যা আপনার অগ্রভাগ নির্বাচনের সাথে গ্যাস প্রবাহ এবং ছিদ্রকে প্রভাবিত করে।
এটি মনে রেখে, নিশ্চিত করুন যে অগ্রভাগটি প্রয়োগের জন্য যথেষ্ট বড়। সাধারণত, বড় তারের মাপ ব্যবহার করে উচ্চ ওয়েল্ডিং কারেন্ট সহ অ্যাপ্লিকেশনের জন্য বড় বোর মাপের অগ্রভাগের প্রয়োজন হয়।
আধা-স্বয়ংক্রিয় ওয়েল্ডিং অ্যাপ্লিকেশনগুলিতে, পর্যায়ক্রমে অগ্রভাগে ওয়েল্ডিং স্প্যাটার পরীক্ষা করুন এবং ওয়েল্ডারের প্লায়ার (ওয়েলপার) ব্যবহার করে অপসারণ করুন বা প্রয়োজনে অগ্রভাগ প্রতিস্থাপন করুন। এই পরিদর্শনের সময়, নিশ্চিত করুন যে যোগাযোগের টিপটি ভাল অবস্থায় আছে এবং গ্যাস ডিফিউজারে পরিষ্কার গ্যাস পোর্ট রয়েছে। অপারেটররা অ্যান্টি-স্প্যাটার যৌগও ব্যবহার করতে পারে, তবে তাদের অবশ্যই খেয়াল রাখতে হবে যে অগ্রভাগটি যৌগের মধ্যে খুব বেশি বা খুব বেশি সময় ডুবিয়ে না রাখবে, যেহেতু যৌগের অত্যধিক পরিমাণ শিল্ডিং গ্যাসকে দূষিত করতে পারে এবং অগ্রভাগের নিরোধক ক্ষতি করতে পারে।
রোবোটিক ওয়েল্ডিং অপারেশনে, স্প্যাটার তৈরির বিরুদ্ধে লড়াই করার জন্য একটি অগ্রভাগ পরিষ্কার করার স্টেশন বা রিমারে বিনিয়োগ করুন। এই পেরিফেরালটি উত্পাদনে নিয়মিত বিরতির সময় অগ্রভাগ এবং ডিফিউজার পরিষ্কার করে যাতে এটি চক্রের সময়কে প্রভাবিত না করে। অগ্রভাগ পরিষ্কারের স্টেশনগুলি একটি অ্যান্টি-স্প্যাটার স্প্রেয়ারের সাথে একত্রে কাজ করার উদ্দেশ্যে তৈরি করা হয়েছে, যা সামনের উপাদানগুলিতে যৌগের একটি পাতলা আবরণ প্রয়োগ করে। খুব বেশি বা খুব কম অ্যান্টি-স্প্যাটার তরল অতিরিক্ত পোরোসিটি হতে পারে। অগ্রভাগ পরিষ্কার করার প্রক্রিয়াতে এয়ার বিস্ফোরণ যোগ করা ব্যবহারযোগ্য জিনিস থেকে আলগা ছিটা পরিষ্কার করতেও সাহায্য করতে পারে।
গুণমান এবং উত্পাদনশীলতা বজায় রাখা
ঢালাই প্রক্রিয়া নিরীক্ষণের যত্ন নেওয়া এবং ছিদ্রের কারণগুলি জেনে, সমাধানগুলি বাস্তবায়ন করা তুলনামূলকভাবে সহজ। এটি করার ফলে আরও বেশি আর্ক-অন সময়, গুণমানের ফলাফল এবং আরও ভাল অংশগুলি উত্পাদনের মাধ্যমে চলমান নিশ্চিত করতে সহায়তা করতে পারে।
পোস্টের সময়: ফেব্রুয়ারি-০২-২০২০